TISCO: The World's Most Cost Effective Steel Plant
|
|
ICMR HOME | Case Studies Collection
Case Details:
Case Code : OPER011
Case Length : 12 Pages
Period : 1980 - 2002
Organization : TISCO
Pub Date : 2002
Teaching Note : Available
Countries : India
Industry : Steel
To download TISCO: The World's Most Cost Effective Steel Plant case study
(Case Code: OPER011) click on the button below, and select the case from the list of available cases:
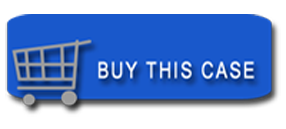
Price:
For delivery in electronic format: Rs. 300;
For delivery through courier (within India): Rs. 300 +Shipping & Handling Charges extra
» Operations Case Studies
» Case Studies Collection
» ICMR HOME
» View Detailed Pricing Info
» How To Order This Case » Business Case Studies » Case Studies by Area
» Case Studies by Industry
» Case Studies by Company
Please note:
This case study was compiled from published sources, and is intended to be used as a basis for class discussion. It is not intended to illustrate either effective or ineffective handling of a management situation. Nor is it a primary information source.
Chat with us

Please leave your feedback
|

<< Previous
Excerpts
Implementing Best Practices
In 1999-2001, TISCO took measures to reduce costs further by adopting innovative
strategies and other cost-cutting exercises. For example, TISCO stopped using
manganese, an expensive metal used to increase the strength and flexibility of
steel. The company made efforts to reduce its product delivery time from 3-4
weeks in 1998 to 2 weeks in 2000. The company aimed to further reduce the time
to one week.
TISCO also took steps to reduce its manpower costs. Between 1996 and 2000, TISCO
reduced its workforce from 78,000 to 40,000 employees. Analysts opined that
cutting its workforce by 38,000 employees was not an easy job and the company
was able to do it with a lot of communication with employees.
|
|
TISCO had adopted Performance Ethic Programme (PEP), under which, it planned to
promote hardworking young people to higher positions depending on their
performance, rather than following the convention of seniority. This
exercise was expected to cut the management staff from 4000 to 3000. PEP had
two core elements. Firstly, it proposed a new organizational structure,
which was expected to foster growth businesses, introduce more
decision-making flexibility, clear accountability, and encourage teamwork
among the managers and the workforce...
The Future
Analysts felt that TISCO's modernization program was very successful. The
Steel Authority of India Ltd. (SAIL) adopted a similar program with an
investment of Rs 70 billion. However, the program was not successful. In
contrast, in spite of the depressed market and lower margins, the decrease
in the production costs enabled TISCO to achieve a profit after tax of Rs
5.53 billion in 2000-2001, and Rs 4.22 billion in 1999-2000 compared to Rs
2.82 billion during 1998-99 (Refer Exhibit VII)...
|
Exhibits
Exhibit I: Steel Product Categories
Exhibit II: Tisco's Modernization Program
Exhibit III: Tisco: Phase V Modernisation
Exhibit IV: Total Operational Performance (Top) Program
Exhibit V: Top Aims at All-Round Performance Improvement that is both
Dramatic and Continuous
Exhibit VI: Formal Top Process: An Overview
Exhibit VII: Income Statement |
|
|